Monday, July 25th, 2011
Today, Innovalight’s founders and investors are celebrating the company’s official acquisition by chemical giant DuPont. Terms of the deal were not disclosed, but Innovalight should have been able to negotiate from a position of strength due it’s selective-emitter (SE) ink technology being taken up by JA Solar, Jinko, Motech, and Yingli among other crystalline-silicon (c-Si) photovoltaic (PV) manufacturers.
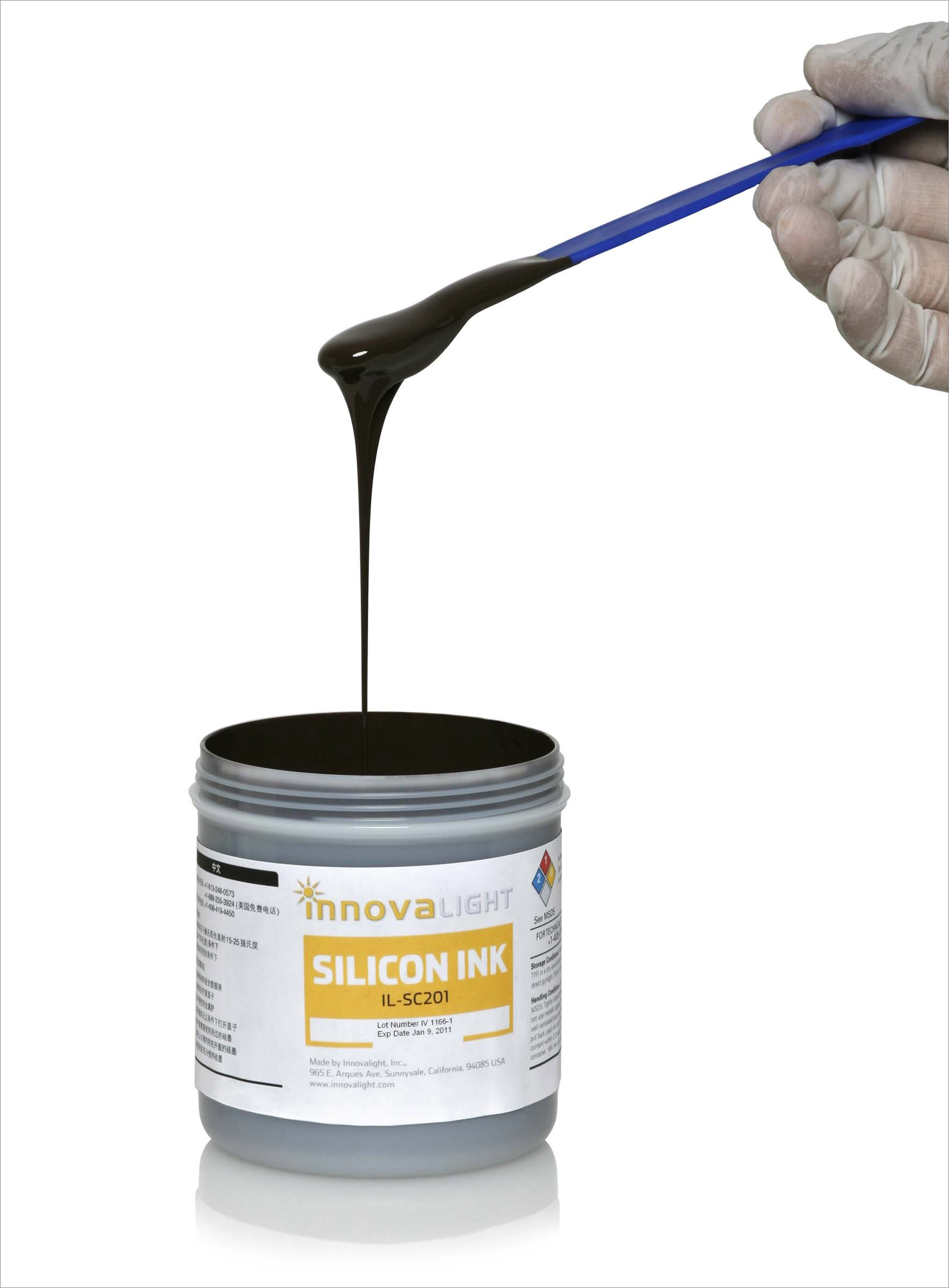
Doped-silicon inks from DuPont Innovalight enable the production of selective emitter solar cells with the addition of a single screen printing step.
Innovalight based in Sunnyvale, California has developed a functioning “solar ink”-composed of phosporous-doped silicon nanoparticles-that can be screen printed to form SE regions in a single additional step as part of a c-Si PV fab line. DuPont, based in Wilmington, Delaware, earned more than $1 billion in sales revenue in the photovoltaic market in 2010, much of it revenue from the company’s “Solamet” line of silver metallization pastes.
Since the advantage of SE in PV cells is found in integration with the top-side metalization, DuPont’s PV metallization paste expertise should allow the company to optimize integration with SE inks. According to industry estimates, SE technology could represent 13 percent of crystalline silicon solar cell production by 2013 and up to 38 percent by 2020.
“Innovalight brings in-depth knowledge of solar devices, silicon technology and Selective Emitter technology, and DuPont adds expertise in materials science, manufacturing capabilities and global market access,” said Conrad Burke, founder – Innovalight. DuPont experience in production scale-up and manufacturing operations will accelerate time-to-market for Innovalight products and broaden customers’ access to the technology.
JA Solar vouches for Innovalight
At the Spring 2011 Materials Research Society meeting in San Francisco (C4.2), Yong Liu of JA Solar presented an invited paper on “Comparative Study on Manufacturability of Selective Emitter and Double Printing,” based on the Innovalight ink for SE.
The phosphorous-doped ink is screen printed prior to blanket phosphorous deposition, such that n++ silicon is formed where contacts will be later printed while n+ remains across the rest of the wafer surface:
- Surface Texture etch,
- Ink print and bake [the only new step],
- POCl Diffusion (tube furnace),
- Plasma edge isolation/glass-removal,
- PECVD SiNx ARC/passivation.
- Metallization printing back and front,
- Furnace firing, and
- Testing binning.
The SE process is robust and cost-effective. “We’ve demonstrated 1.2% absolute efficiency gain in our R&D lab,” said Liu. “In manufacturing we can get around 1% absolute efficiency gain, with cells off of the line showing about 18.5 percent median efficiency ignoring low outliers due to poor wafer quality.” The selective emitter structure reduces surface recombination losses, and so improves the spectral response at short wavelengths. SE reduces contact resistance from ~80 Ohms/sq to 65 Ohms/sq, compared to ~70 Ohms/sq as the practical limit for mass production using POCl alone.
The double-printed front contact allows for the fingers to have much higher aspect-ratio and improved conductivity. The maximum height in a single screen print is generally 18-20 microns, while double-printing can get to ~30 microns height for ~30 microns width, corresponding to an increase in the fill-factor from ~78% to ~80%. The printing process happens every 3 seconds, and the screen must be very rigid so stainless steel actually deforms too much in HVM, and improvements are needed to be able to do double-printing.
JA Solar ran 100k wafers (3 days production) comparing SE and DP, and the cell-level efficiencies were 18.6 and 18.2 percent (respectively). Double-printing seems to be redundant when SE is already in use. “The reason is that the SE underneath sheet resistance is very low, so you don’t need double-printing and it’s kind of redundant,” explained Liu. —E.K.
Tags: c-Si, deposition, double-print, DuPont, efficiency, fab, HVM, ink, Innovalight, integration, JA Solar, materials, Motech, MRS, POCl, PV, screen print, SE, selective emitter, silicon-ink, Yingli